Deck Glassing Hatches and Vents
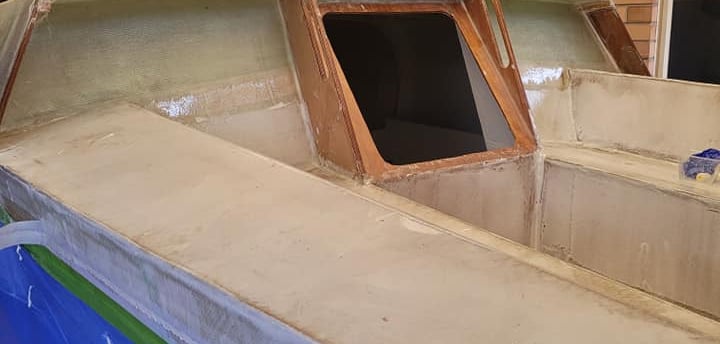
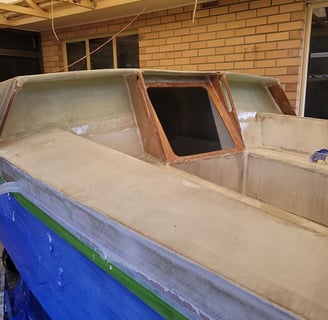
Another significant amount of time has passed since my last post so it has been on my mind for a while to provide a bit of an update where things are at. Following my last post where I had plated the deck it was time to get started with the fibre glassing so the first step was to epoxy glass tap to all the deck chines. Once dried the edges were all sanded to take out any hard edges and make a smoother transition for the deck glass.
Following this I made a few changes to the compannionway to ensure once the hatch was fitted it would be able to swing out with out getting caught on the deck overhang. I also added an extra length of ply to the overhang to allow for extra strength for fitting winches in due course.
The next step was to lay the deck fibreglass making sure there were not bubbles and the glass was layed out well. For the majority of the deck I used a 45 double bias @435g although I decided to use a triple bias 1151g over the portion of the deck where the winches / clutches etc are located.
While the glass was still 'green' I went straight to work with filling with a thickened West System Epoxy mix. Following this process was the time consuming part... Fairing! Given all the corners in the cabin, this was probably even longer than expected however bit by bit I kept chipping away (with a bit of help from family and friends from time to time). For this stage I used the same method as the hull in which I would sand the deck back as best possible, making sure I didnt keep sanding through raw fibreglass and then filling all the low spots before repeating the process.
Other little jobs were completed throughout the fairing process as well which included framing up the hatches and making up the mast step. The step was made out of solid fibreglass and epoxy which was constructed by using a plastic lunchbox of all things which had the same measurements as shown in the plans for the step. I then layed 4-5 layers of glass at a time down and filled with West System Epoxy until it was semi cured before adding several more layers and repeating the process until I had the correct thickness. It was then simply a matter of shaving off the top until it had the right shape with a grinder and electric sander and then epoxying to the hull.
The last step of the fairing process when I was confident it was at about 90-95% was to add the 'high-build' epoxy paint. I used a couple of green coats initially as a base so I knew that when I was sanding and hit green to stop so I wouldn't keep sanding down to raw fibreglass.
I then added 3 coats of white prior to adding blue guiding paint to see where the low spots were when sanded which were then filled with International Interfill. I repeated this process 3 times before I was happy with the job. Finally, fairing done!
With the fairing done, the next job on the list was add the final coats of paint. I used an International perfection system for this process and ended up rolling on 3 coats of undercoat and 2 coats of the final overcoat. I then finished off with 3 coats of high-vis paint the sheer strakes to finish off the boat which was a pretty exciting moment.
From there, I started fitting the boat out with the bubble and the hatches. Lewmar low profile hatches were used across the deck with a Size 60 for the compannionway, a 40 for the forward hatch and a 20 in the middle which after a bit of thought was installed with the opening towards at the bow. There is a bit of discussion which way to install this but I went with the option that will allow the most air flow over being able to keep the hatch open longer in foul weather. I also installed the 1RE size to the sheer strakes for portlights.
Other fittings installed to date include the bubble which has dimensions of 500mm x 10mm thickness with a 50mm flange. I also had this tinted to hopefully help reflect heat. My compass is a Plastimo contest 101 and a model which allows to be installed on a bulkhead between 10 - 25 degrees. The winches installed are Andersen 12 Self-tailing and the rope bags are Ronstan bags 400mm in length for those above the seats and 500mm in length below the compannionway. I ended up going with these as I preferred a mesh that allowed easy removal of water as opposed to bags that are more enclosed. For the vents I have used 2x Stainless Steel Mushroom vents which have been placed on frame S as close as possible to the centreline and a large Plastimo dorade box vent to the deck. Lastly, Ive installed some high quality access hatches below deck now so am looking forward to loading the boat up with all the gear shortly. Next steps, include chipping away at the fitout whilst I wait for the Stainless Steel package which has been ordered from the great Piotr in Poland!