Stage 4- Hull Epoxy and Fairing
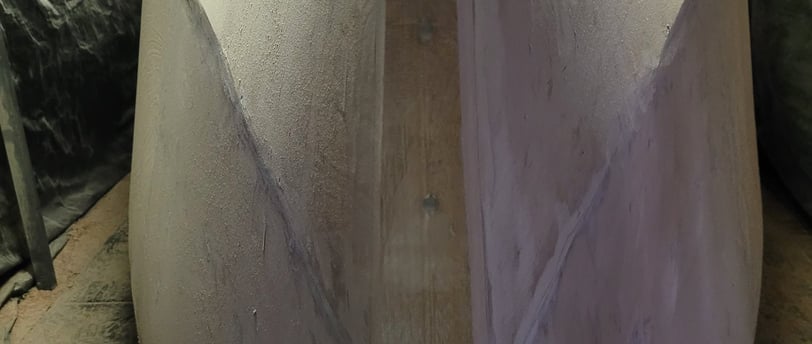
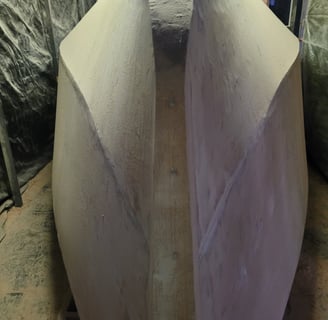
Over the past few months I feel like I have picked up the pace. Looking at the boat it may not look a great deal has been done but I can assure the work has been put in!
Following completion of the hull plating stage, it was time to get setup and get the fibre-glassing done.
After confirming with Class Globe management that a single layer of 0 & 45 degree directional reinforcement 1151g/m² Triaxial cloth would be suitable (being very slightly under the recommendation) I made my order with Australian Made Colan cloth whom I understand have a great reputation for high quality glass in this part of the world.
Whilst there were some queries floating around that the cloth may be too thick to get around corners and soak up too much epoxy, I never had any dramas.
In preparation of laying the cloth, I rounded off the chines quite substantially to mitigate any issues of bubbling on the edges and ensured the panels were as true as possible by adding some thickened West System epoxy to various low spots across the boat. Once I was happy where it was at it was time to lay the sheeting.
Prior to the glassing day I had measured and cut out each panel starting at the transom and then working my way forward with the centre of the boat to the longest portion of the panel being the measurement for the associated panel. To further clarify, towards the stern of the yacht, the front of the panel was the measurement taken and towards the bow, the measurement was taken from the rear of the panel. 150mm was added to the middle of the underside of the boat for an appropriate overlap and a further approx. 150mm was added to the length at the gunwhale to ensure each panel was long enough. I then pulled out approx 5cm of the 0 degree uni-directional reinforcements on each end so there would not be substantial overkill/fat on the overlay portions of the panel. Further, each panel was labelled 1 through to 11, 1 being the transom then 2-11 being the side panels and then rolled up in preparation for glassing day.
My good friend and Shipwright Tommy Crabb offered to come help me for the day, and a big day it was. Our method of laying the sheeting started with substantially wetting out the bot where the panels would sit individually, starting from the transom and then working our way forward. Once the associated portion of the boat was wet, the corresponding sheet went on and then West System Epoxy was rolled into the sheet until it was appropriately soaked paying particularly attention to the chines to ensure there was no bubbling coming out from underneath.
The Panels required a bit of manipulation particularly towards the bow to sit well on the boat but in general was quite a simple process. The last thing Tom did was use stainless steel roller that went over each sheet individually to ensure it was sitting well. Right on the bow section we also decided to swap the thick glass out to a thinner stitched double bias glass (435g/m²) That I had purchased for the deck and overlayed three layers. This was layed across the bow, working back with each layer overlapping 300mm or so. In summary the bow has over 1,300g/m² glass across it (minimum), well above the associated requirements. To cap the process off, each of the overlays had a strip of peel-ply set across them. I have noticed a lot of other builders applying peel ply across the whole boat however we did not go down this path.
Several hours later while the glass was still 'green' I got straight into the filler albeit it was the following day by this stage. West System Epoxy was mixed with a Q-Cell Filler and a small amount of west system fibre as well. In general I made up 500gm epoxy batches that needed around 5 cups of Q-Cell and 1 Cup of Fibre. In total, I ended up using around 7kgs across the boat and after being up for 2 days straight, I was cooked but a happy man. Lock and Load!
The next weekend, the sanding started but not before I was advised that I had missed out on a required part of glassing. Extra strips of glass on the chines!!!! It was the first time of the build where I had realised I had made an error. This was a part I had overlooked in builders discussions and having not looked at the plans for a number of weeks it was simply overlooked. Upon requesting of management if it was ok to move on, I was requested to contact the designer Janusz for clarification. After several emails it was determined to add the extra required 600g/m² strips or x2 overlapped as required in line with the plans to the outside of the already applied fibre glass. Sanding back the filler to add these sent me flat for a few weeks as I felt like I was going backwards but I got the job done in the end and Janusz was comfortable with this process.
I quickly learnt throughout this process takes a lot longer than anticipated but I knuckled down over the coming weeks to get the fairing done. After the first lot of sanding with 40 grit, another lot of filler was added, before more sanding, another lot of filler, then more sanding. Throughout that the later filling stages I also re-sharpened the chines towards the stern of the boat, the idea being water would be hitting the boat at the bow on a curved chine and exiting on a sharp one. This is much like the sailing dinghy's I grew up with.
Following a few rounds of filler, I moved on to sanding with a 80 grit board. After cleaning the boat off, 2 coats of a green ppg epotec high-build primer were rolled on with a 160mm (4mm nap) roller followed by 4 white coats to commence the finer detail. Again, sand, fill, sand, fill, sand, fill this time with the epoxy high build as opposed to the filler. After each coat I applied International guiding coat to determine where the low spots were and filled those up with International 833 finishing filler. When sanding back I would know when to stop when I hit the green epoxy as I didn't want to go back to the bare fibreglass.
After several big weekends the filling stage and therefore stage 4 of the project was finally done. Time to move on. Yew!!!!