Stages 5 & 6- Roll Hull, Internal Fit-Out & Deck Plating
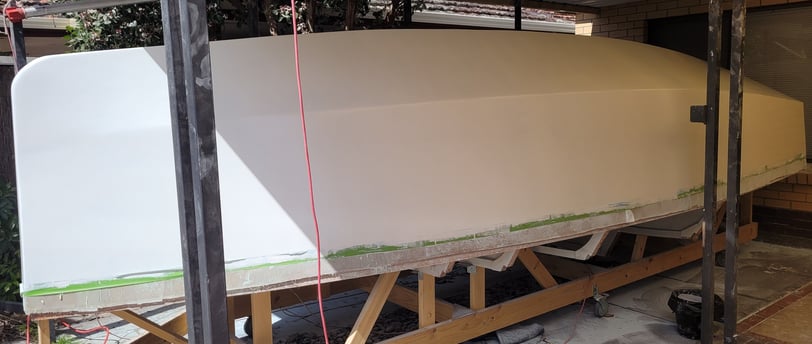
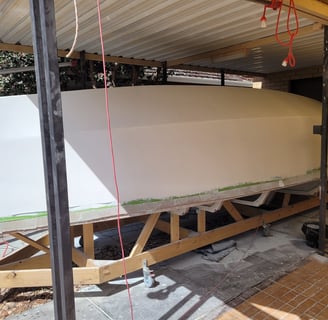
It’s been a long time since my last post…
From work, sport and family commitments, my schedule remains full however my passion for completing Hull #05 now named ‘Immortal Game’ has not waivered. The weather in recent months here has been average however I continue to make progress most weekends albeit slowly.
Picking up from when I last left off, the boat is far more advanced into the build and am now in the process of finalizing stages 5 and 6 of the building processes being roll hull, internal plywood fit, crash box and deck plating. At the time of writing this update I have yet to glass and fair the deck so will put some detail up about that at a later stage.
Following the fairing of the hull and loading the boat up on my mate Toms trailer to head to his farm and complete the rolling process the boat spent a couple of weeks out there until timing allowed for us to get the job done. When I got there, Tom explained the plan of using straps and the family’s forklift which would simply entail rolling it over with the jig in place very slowly and making the necessary adjustments as it went over to ensure the boat didn’t hit the ground. I had hold of a line to assist the boat movement and slowly but surely, we got the job down and laid the boat on its hull on some foam mates whilst we then worked on removing the jig. Once this was off, we cut off the upright portions, layed down a couple of extra planks on the base and then used the forklift again on the re-purposed jig. When the boat was in place, we then loaded it back up onto the trailer and made the trip back home and put it back in place by slowly releasing the boat down the tilted trailer slowly. The pictures below show the process that was done.
The first task, once the boat was up the right was, was to tidy up / sand some average spots I had done with the epoxy which I didn’t notice until it was in the sunlight and fillet the rest of the areas I had missed when the boat was upside down. From there I started at the bow with the crash box requirements. The main crash box compartment was already in place as it is a standard inclusion with the kit and the small forward crash box piece comes cut, ready to go.
After testing the panels sizes were correct, I installed / epoxied the small forward crash box compartment and forward bunk piece before cutting out two circle pieces with a hole saw attachment on a drill to gain entry into each of these compartments. From there, I filled each of these up with a non-porous expanding foam that was quite interesting to watch. I could see the foam creeping out into all the extremities of the space before looking for an exit which was the cut-out holes at the top. Once the foam was set, I then trimmed back the foam and epoxied the cut-out portions back in place prior to covering with a layer of glass to give extra strength to that area.
From there I dry fitted a compact toilet (which I am considering installing underneath the front bunk) to see how that would fit and then worked on making up custom bunk pieces that would surround that toilet, bring extra strength to the front of the boat (although not compulsory if a toilet is fitted, I understand) and create extra storage space / bulkheads to each side of the boat. This was all done with 9mm Ply.
After I had finished in the bow, I moved to the stern of the boat and started working in the cockpit. The first job completed back here was to split up the back bulkheads into three separate compartments, which is not compulsory but something I wanted to do after discussions with some other builders. This was done by simply extending a ply portion essentially directly underneath the vertical uprights (see picture) on either side which were already in place from a previous part of the build. After this was done, I installed the cockpit pieces as per the plans, although I intend to do some install some form of strengthening / backing plates in certain places down the track.
I then added the backing panel for the skeg and then carefully measured up where the holes were to be placed. Back in the initial stages of the build I had actually commissioned a friend of another Japanese builder (Shinichi Sonoda) to construct the skeg for me along with a rudder, bow sprit and dagger boards as these were some more intricate pieces, I wasn’t sure I had the skill to build myself at that point of time of the build. It was just up to me to fill the middle with chopped up fibre and epoxy which was fine although if I had my time again, I would have filled it up slightly slower. I did do it over 5-6 fills however if I put in too much at a time it would get very hot which I am sure would be better to avoid.
Anyway, once it was ready to install, oversize holes were nervously cut out of the bottom of the hull and were filled with thickened epoxy which was also applied to the bottom of the skeg and sanded hull where it was to be attached. Tape was over the bolt threads as to not get any epoxy on them and then with the help of the wife we located the bolts in the middle of these oversize holes and attached it in place with large SS 316 washers and nuts to let it all set.
From there I moved to the cockpit floor. As I was of the opinion that this space would be better off as being buoyant that anything else and that I had plenty of left-over foam, I decided to completely fill it up. Instead of cutting holes in what would be the cockpit floor however and due to the large space, that required filling, I simply filled the open space until it was overflowing and trimmed it back to a point in which the cockpit floor could be installed. Once this was done it was a job of filleting all the edges and covering all the ply with a layer of epoxy to stop outgassing when it comes to applying the glass down the track
The next step was to move into the cabin and start working on the fit out of the ‘open living area’. My fit out is largely by purpose going to very basic to meet the building requirements and provide some storage space. This is both due to keeping the boat as light as possible and also not to add much complexity to the build.
The berths were installed the whole way from the rear bulkhead to the D frame with no cutout for the nav table area which some builders have done. Possibly slightly less comfortable at sea but I figure would give extra strength to the boat and is consistent with plans. Once the bunk tops were in, I added some upright floor to ceiling pieces, mainly as I had seen this done on Don’s boat and installed a basic galley area. The pictures below show how it ended up. I am leaving the nav area open for now until I decide how to best install the electrical system and provide some space for this process in due course.
For the sides I’ve used a 6mm Ply (the only of this size used so far to date) to install a couple of basic panels which will provide storage area and as advised will be a requirement for the build from my understanding. I still need to do a bit of work on these but at lease wanted to get the basic structure of it in for now. I also cut out holes on either side of the S frame with a hole saw piece and added a ply piece underneath to provide a couple of gear stuff holes which Don had mentioned in a previous video and has included on Trekka.
Next, I moved onto the companionway and worked on installing a custom hatch. Given that I still had the base ‘S’ frame installed with a section ready to start on the standard hatch, I cut this down to accommodate a flush deck which I was going with including a bubble. Once this was tidied up, I then basically copied a set up that I had seen from photos and making queries with another builder, the mighty Igor Carretero from his boat in Spain albeit for a few of my own small ideas. This companionway is now setup for a size 60 Lewmar Hatch that will provide a waterproof entry into the boat and for the most part I am happy with the result. My only reservations are the angle of the hatch and that I am now anticipating when opening the lid, that the overhang I am looking to have on the deck may not allow it to be opened. This being said I will need to just shave back the top of the deck ply a bit until it is able to be opened. For the step leading into the boat, I have simply epoxied two pieces of ply together and placed at bunk level inside the companionway as I am considering not having any upright panels whatsoever here for very easy access to the liferaft. It is likely I will just have some form of easily release straps here that can be pulled to enable me to pull out the raft however haven’t thought about that in too much detail to date.
Now, it was time to move onto the deck. First, I needed to install the deck frames in place which was somewhat time consuming as there is a bit of custom detail that goes into these depending on the type of overall deck that you are looking for. For me I needed to ensure the frames were well placed around the hatches and where the bubble would be located. This also meant that a couple of the standard CNC pieces that I had were not the correct size and so I needed to order some more timber to get the job done. Once this was completed the majority of the time was spent in preparation to make that the deck panels would fit well to the frames etc. This meant shaving off some of the frames to fit and levelling out in particular the D Frame which needs a bit of work so that the plating would fit.
Before epoxying the plating down, I also installed a Lewmar Size 70 Medium Profile Hatch to the D frame which was the largest ‘standard’ hatch I could find that would fit and was able to get my hands on in a reasonable time period. Once ready it was time to finally put the deck on which was a great moment! With all the prep work done this was a simple process however I was required to wait for several weeks for 2 new 9mm sheets to arrive as I was intending on having a 16cm or so overhang from frame ‘S’ similar to Don’s boat which would house the winches or at the least provide a bit of extra protection to any plotters etc that might be installed on the S frame. I had also used a lot of the excess ply up on the internal fit out and would have been needed anyway. It was just a pain that they were needed at a time when there was little ply anywhere in Australia and was quite costly to get even a small amount delivered.
Since the deck panels have been epoxied in place it has been a matter of planning, sanding and tidying these up as best possible in preparation for the glassing stage which is imminent at the time of writing this blog. Again, I’ve continued to use West System Epoxy to date (with a slow hardener), attached panels with 316 screws, primed them with International Everdure (on the inside of the boat) and epoxy on the outside. Inside priming and painting has all been done with PPG Epotec and filleting / tidying up / levelling panels etc was either done with West System with a 413 microfibre blend or International Interfill for some of the smaller jobs.
I hope this blog provides a basic reference or is of use to some and will write about the next stages hopefully in the not too distant future!